Sommerbesuch von Glas Nowak in Marl Brassert
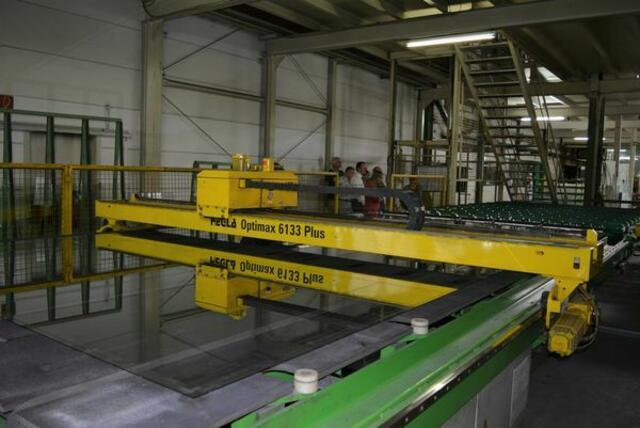
- Riesige Maschinen schneiden das Glas Millimeter genau zurecht. Foto Stadt Marl.
- hochgeladen von Siegfried Schönfeld
Drei Standorte, 700 Mitarbeiterinnen und Mitarbeiter, darunter 15 Auszubildende – beeindruckende Zahlen, die Geschäftsführer und Firmen-Chef Christian Nowak den Ratsmitgliedern und der Verwaltung gleich zu Beginn des Besuches präsentierte. Allein am Standort in Marl werden täglich mit fast 120 Arbeitskräften rund 1.500 hochwertige ISOPANE-Funktionsisoliergläser auf drei Produktionslinien im Mehrschichtbetrieb für den deutschen (vor allem Münsterland, Ruhrgebiet und Rheinland) sowie dem niederländischen Markt gefertigt.
Firma in der dritten Generation
„Der Markt verlangt heute aber deutlich mehr Alternativen. So bieten wir auch Glas für den Interieur- und Exterieurbereich genauso an wie Beschläge, zum Beispiel für den konstruktiven Glasbau, den Innenausbau oder die Sanitäranwendung und hochwertige Glaslackierungen mit einem umfangreichen Gestaltungsspielraum auf der Glasfläche“, sagt Christian Nowak, Enkel des Firmengründers Josef Nowak und somit die dritte Generation des 1964 in Bochum-Wattenscheid gegründeten Unternehmens.
Unternehmen möchte in Marl expandieren
Deshalb würde das Unternehmen gerne expandieren – am liebsten in Marl. Ist das Firmengelände aktuell etwa 15.000 Quadratmeter groß, wünscht man sich bei Glas Nowak 40.000 bis 50.000 Quadratmeter Fläche, um auch weitere Arbeitsplätze zu schaffen.
Beginn im eigenen Wohnzimmer
Angefangen hatte alles direkt nach dem Krieg. Als Flüchtlinge aus Oberschlesien fand Christian Nowaks Großvater mit seiner Familie in Bochum-Wattenscheid ein neues Zuhause. Schnell erkannte der Glaser, welches Potenzial die Region für ihn bot. Am heimischen Wohnzimmertisch wurden die ersten Glasplatten geschnitten, später in der Garage die ersten Isoliergläser per Hand gefertigt. Dank der Flexibilität und schnellen Lieferzeiten (nur wenige Tage im Vergleich zu sechs bis acht Wochen in der Industrie) wuchs der kleine Familienbetrieb ab Mitte der 1960er-Jahre zum mittelständischen Unternehmen.
Unterschiedliche Arten von Isolierglas (Wärme-, Schall-, Sicherheits- und/oder Sonnenschutz), Sicherheitsglas (Einscheibensicherheits- und Verbundsicherheitsverglasungen) und Basisglas, wie z. B. Floatglas, Gussglas und Dekorglas gehören heute zum Produktionsumfang der Gruppe.
Mit Christian Nowak, Geschäftsführer Maik Tobias und Prokurist André Reidl ging es durch die Marler Produktion. Riesige Schneidemaschinen dominieren die Hallen, um die 6 x 3,21 Meter großen Glasplatten individuell je nach Kundenwunsch zurechtzuschneiden. „So landen unsere Produkte dann schon mal im Berliner Reichstag oder im britischen Parlament“, verrät Maik Tobias. Aber auch die Möbelindustrie oder Kunstglasereien sind Kunden.
Qualitätsprobe per Laser und Auge
Zurechtgeschnitten geht es für das Glas in die Weiterverarbeitung zu Isolierglas. Hier wird das Glas mit Spezialbürsten und -maschinen gereinigt, um am Ende noch einmal einer Qualitätsprobe unterzogen zu werden – per Laser genauso wie mit dem menschlichen Auge und anschließend zu Isolierglas weiterverarbeitet. Bestimmte Ausführungen und Formen werden noch per Hand versiegelt.
Insgesamt 250 bis 300 Tonnen Glas werden pro Tag innerhalb der Nowak-Glas-Gruppe verarbeitet, und allein am Standort Marl können Isoliergläser mit einer Größe von bis zu 2,70 x 5,00 Meter gefertigt werden. Die Stimmung in der Produktion ist bei den Angestellten locker und gelöst. „Unsere familiäre Atmosphäre ist Teil der Motivation. Denn wir wünschen uns, dass die Mitarbeiterinnen und Mitarbeiter mit einem Lächeln zur Arbeit kommen“, lautet Christian Nowaks Philosophie.
FAKTEN ZUR GLASHERSTELLUNG
Glas Nowak ist am Glashersteller Euroglas beteiligt. Dort wird das sogenannte Floatglas hergestellt. Ein Gemenge aus Altglas, Kalk, Soda und Quarzsand als Hauptbestandteil wird bei 1550 Grad geschmolzen, anschließend auf einer flüssigen Zinnoberfläche ausgebreitet. Glas ist leichter als Zinn und schwimmt entsprechend auf dem Zinn, kann sich dort gleichmäßig ausbreiten. Zur Formgebung wird es auseinandergezogen oder gestaucht (je nach gewünschter Stärke). Danach werden die riesigen Elemente auf einer Strecke von 100 Metern von 600 auf 60 Grad heruntergekühlt und zugeschnitten. Schließlich wartet der Weitertransport zu den verarbeitenden Betrieben – so wie in Marl.
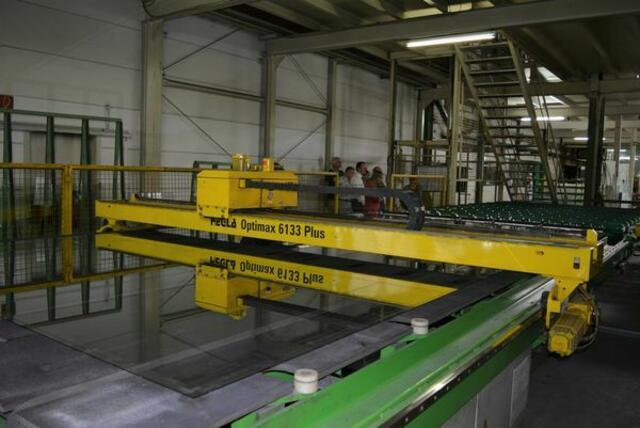
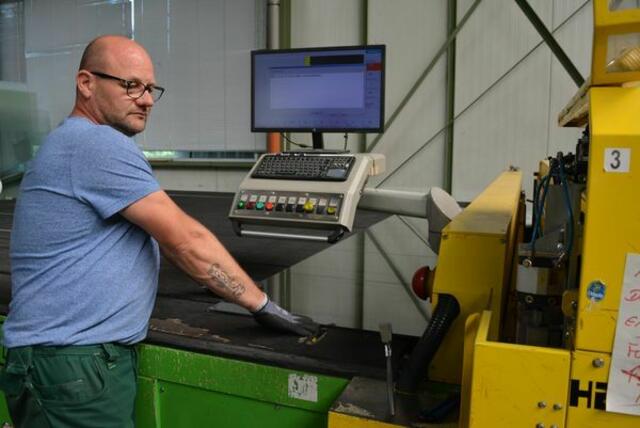
Autor:Siegfried Schönfeld aus Marl |
Kommentare
Sie möchten kommentieren?
Sie möchten zur Diskussion beitragen? Melden Sie sich an, um Kommentare zu verfassen.