Weseler Unternehmer an der „Wiege“ des Stahls
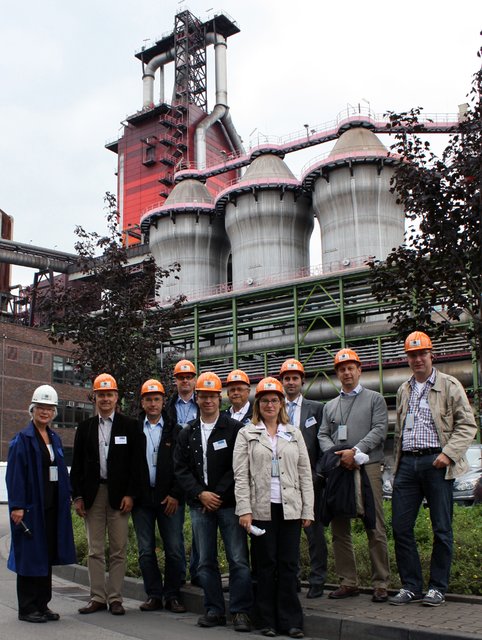
- Markantes Bauwerk an der A 42 - Die Mitglieder des Unternehmerverbandes aus dem Kreis Wesel erkundeten bei ThyssenKrupp Steel auch den neuen Hochofen, der mit dem in Duisburg hergestellten, eingefärbten Stahl verkleidet ist.
- Foto: (Foto: Unternehmerverband)
- hochgeladen von Harald Molder
Wie aus Eisenerz funkensprühend und tonnenweise Stahl „made in Germany“ wird, erfuhren Geschäftsführer aus dem Kreis Wesel in dieser Woche bei ThyssenKrupp Steel Europe in Duisburg. Die Unternehmer, die den Produktionsprozess vom Wareneingang bis zum noch rot glühenden Coil verfolgten, waren der Einladung des Unternehmerverbandes gefolgt, der regelmäßig zu solchen Netzwerk-Treffen einlädt.
„Wir haben viele Industriebetriebe in unseren Mitgliedsreihen, die Stahl weiterverarbeiten. Sie wollten wir an die ‚Wiege‘ des Werkstoffes bringen“, sagte Martin Jonetzko, stellv. Hauptgeschäftsführer des Unternehmerverbandes.
Für die Duisburger gehört Thyssen zu ihrer Stadt wie Rhein, Köpi und MSV. Dennoch hat sich in der Geschichte der Stahlproduktion eine Menge verändert: Heute investiert „TK“ rund 350 Mio. Euro jährlich in den Umweltschutz, sodass Luft und Wasser rund um die hiesigen Firmengelände sehr viel besser sind als noch vor Jahrzehnten. Auch optisch will ThyssenKrupp das graue Industrie-Image ablegen:
Der neue Hochofen 8 ist mit eingefärbtem Stahl – natürlich im eigenen Hause entwickelt und produziert – verkleidet. Die Unternehmer sahen auf ihrer Rundfahrt zunächst die Warenanlieferung in Schwelgern; Koks und Eisenerz werden dann auf ausgeklügelte und computergesteuerte Weise im Hochofen geschichtet. Das geschmolzene Roheisen wird dann in Torpedopfannen zu so genannten Convertern gefahren, wo es mit Schrott und weiteren Metallen zum Stahl mit den gewünschten Kundenspezifikationen veredelt wird.
Letzte Station der Unternehmer war die Warmbandanlage, in der die „Brammen“, das sind riesige Stahl-Rohlinge, erhitzt und millimeterdünn am laufenden Band ausgewalzt und aufgerollt werden. „Ein beeindruckender Prozess, den wir Schritt für Schritt begleiten durften“, resümierte Jonetzko.
Autor:Harald Molder aus Duisburg |
1 Kommentar
Sie möchten kommentieren?
Sie möchten zur Diskussion beitragen? Melden Sie sich an, um Kommentare zu verfassen.